Die KIEFEL GmbH entwickelt und produziert hochwertige Maschinen für die Verarbeitung von Kunststofffolien. Zu seinen Kunden zählen namhafte Hersteller aus der Automobil-, Medizintechnik-, Kühlschrank- und Verpackungsindustrie.
Mit eigenen Vertriebs- und Service-Niederlassungen in den USA, Frankreich, den Niederlanden, Russland, China, Brasilien, Indonesien und Indien sowie Vertriebspartnern in über 60 Ländern ist Kiefel weltweit vertreten.
Zu Kiefel gehören der Automobilspezialist KIEFEL Automotive s.r.o. mit Sitz in Tschechien, der niederländische Thermoform-Werkzeugbauer Kiefel Packaging BV sowie die österreichische KIEFEL Packaging GmbH, Lieferant für Werkzeuge und Automatisierungslösungen.
Bei Kiefel und seinen Tochterunternehmen sind rund 1160 Mitarbeiter beschäftigt. Die KIEFEL GmbH ist Mitglied der Brückner-Gruppe, Siegsdorf, ein im Familienbesitz befindlicher mittelständischer Unternehmensverbund im Maschinen- und Anlagenbau, mit insgesamt gut 2.500 Mitarbeitern an 29 Standorten weltweit.
Lösungen Wir bieten bei folgenden Bereichen innovative Lösungen an (für mehr Informationen bitte auf die untenstehenden Links klicken): ►Automobil ►Kühlschrank ►Verpackung ►Medizintechnik ►Service
Firmenvideo
Auf die Zukunft vorbereitet - Intelligente Spritz-Streck-Blasformtechnologie sorgt für hohe Flexibilität, Produktivität und Qualität
Honig-, Ketchup-, Spülmittelflaschen, Kosmetik- und Pillenverpackungen oder Babyfläschchen – die Produktvarianten, die auf dem Blowliner der Kiefeltochter Mould & Matic aus dem österreichischen Micheldorf entstehen, sind genauso vielfältig wie ihr Design. Mit der Entwicklung der einstufigen Spritz-Streck-Blasformmaschine hat sich der Kunststoffspezialist einen neuen Markt erschlossen. Obwohl er ein Newcomer in der Branche der Blasformtechnik war, hat der Erfolg nicht lange auf sich warten lassen. Bernhard Hornhuber, Vertriebsmanager Blasformtechnik, hat den Blowliner mit entwickelt und ist zu Recht stolz auf sein „Baby“: „Die Kunden schätzen es sehr, dass sie die komplette Linie – vom Granulat bis zur Verpackung – aus einer Hand bekommen.“ In der Kosmetik-, Pharma- und Lebensmittelindustrie sind die Maschinen inzwischen im Einsatz, die Auftragsbücher sind gut gefüllt und in den Hallen des Österreichers fertigen die Techniker mit Hochdruck weitere Blowliner.
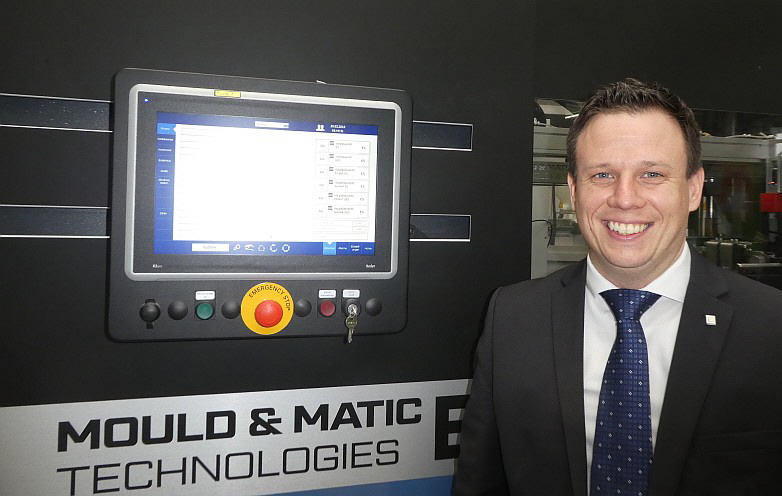 Bernhard Hornhuber, Area Sales Manager Blow Moulding, Mould & Matic Solutions GmbH
In drei Baugrößen steht die Maschine zur Verfügung. Verkaufsschlager ist der Blowliner Medium mit einem Materialdurchsatz von bis zu 130 kg PET pro Stunde. Wie auch der kleinere und größere Bruder verarbeitet er PET, PP sowie HDPE und lässt sich durch die intelligente Konzeption jederzeit auch auf Multilayer-Anwendungen aufrüsten. Vor allem der Premiumsektor, der auf hohe Qualität und Transparenz der Verpackungen Wert legt und bei dem die Stückzahlen zwischen drei und 20 Millionen liegen, schätzt die 1-Stufen-Anlage. Die Gründe bringt Hornhuber auf den Punkt: „Unsere Klientel stellt anspruchsvolle Verpackungen her, die hinsichtlich Transparenz und Dimensionsgenauigkeit hohe Qualitätsanforderungen erfüllen müssen. Meist produzieren die Kunden mittlere Stückzahlen und wünschen sich die Flexibilität, auf der gleichen Maschine unterschiedliche Behälter mit Volumen zwischen 10 Millilitern und fünf Litern zu fertigen. Der Blowliner realisiert all diese Wünsche und trägt so bei unseren Kunden zu einer nachhaltig hohen Anlagenauslastung bei.“
Blick ins Detail Doch wie kann die Anlage den Anforderungen des Marktes genügen? Das verrät ein genauer Blick auf die Konstruktion des Blowliners. Am Anfang der linear aufgebauten Maschine steht die Spritzgießeinheit. Dabei handelt es sich um eine vertikale hydraulische Engel Maschine mit bis zu 4.000 kN Schließkraft und einer Aufspannfläche von bis zu 800 mal 1000 mm – abhängig von der Anlagengröße. Die Plastifiziereinheit verarbeitet PET, PP und HDPE. Hier entstehen die Vorformlinge, je nach Produkt in zwischen acht bis 64 Kavitäten. Jede Maschine lässt sich mit einer Einheit zur Herstellung von Multilayer-Vorformlingen aufrüsten. So können auch Vorformlinge aus PP mit Barriereschichten aus EVOH oder PET mit PA hergestellt werden. Noch warm entnimmt sie ein Linearroboter mit Greifdorn und übergibt die Vorformlinge an die Streck-Blas-Einheit mit einer Zuhaltekraft von bis zu 400 kN.
Die Maschine arbeitet mit ein- bis vierreihigen Blaswerkzeugen, die Vorformlinge mit Durchmessern von 10 bis 150 mm aufnehmen. Jede Kavitätenreihe hat ein eigenes Vor- und Hauptblasventil, sodass sich der Vor- und Hauptblasdruck individuell einstellen lässt. Damit ist es möglich, unterschiedliche Produktvarianten auf einem Werkzeug laufen zu lassen. Die gesamte Streck-Blas-Einheit verfügt über servomotorische Antriebe, die für hohe Wiederholgenauigkeiten, Präzision und Energieeffizienz sorgen. Die Ventiltechnik erlaubt es, den Vor- und Hauptblasdruck in Schritten von 0,1 bar einzustellen. Mit einer kundenspezifischen Blasstudie wird so jeweils bei der Abmusterung die optimale Materialverteilung im Blaswerkzeug festgelegt. Als optionale Prozessüberwachung messen Drucksensoren den Hauptblasdruck, solange dieser ansteht. Fällt der Druck überraschend ab, erhält der Kunststoffverarbeiter sofort eine Alarmmeldung. Wünscht es ein Kunde, kann er den Blowliner auch als Spritz-Blas-Anlage ohne Streckkomponente erhalten.
Nach dem Ende des Blasvorgangs entnimmt der Vakuumgreifer des integrierten linearen Entnahmesystems die fertigen Produkte aus dem Werkzeug und stellt diese präzise auf einem Förderband oder direkt in Kartons ab.
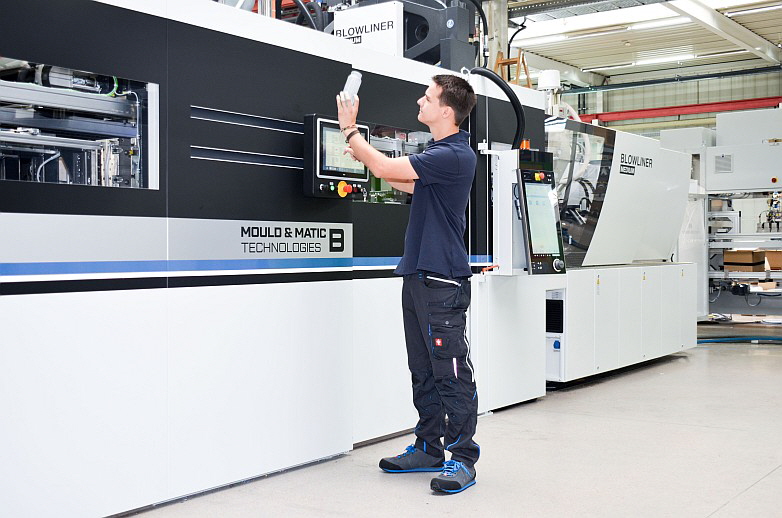 Blowliner M mit einem Materialdurchsatz von bis zu 130 kg PET pro Stunde
Clevere Werkzeugtechnik Viele Überlegungen flossen bei der Konzeption des Blowliners in die Werkzeugtechnik. Hornhuber erinnert sich: „Unser Ziel war es, die Kavitätenzahl und damit die Produktivität bei zusätzlich optimierter Zykluszeit zu bestehenden Anlagen zu erhöhen. Gleichzeitig wollten wir es unseren Kunden ermöglichen, die Maschine optimal auszunutzen. Es sollte möglich sein, sehr unterschiedlichen Produkte, was Größe und damit Anzahl der Kavitäten anbelangt, mit der gleichen heißen Seite des Werkzeuges zu fertigen. Denn dadurch erhält der Anwender eine sehr große Flexibilität in seiner Fertigung.“ Die Lösung liegt in einem ausbalancierten Heißkanalwerkzeug mit Nadelverschlusssystem. Bei jeder neuen Bestellung steht eine Frage im Vordergrund: Welche Produkte will der Kunde heute auf der Maschine fertigen und wie sieht die Zukunft aus? Selbst wenn zunächst ein zweireihiges 12-fach Werkzeug für Produkte mit einem Artikelgewicht von 15g gefahren wird, kann die gleichen heiße Seite später für Produkte aus PET, PP oder HDPE mit beispielsweise 35 g Artikelgewicht eingesetzt werden. „Der Kunde ist auf die Entwicklungen der Zukunft vorbereitet und kann schnell auf neue Herausforderungen reagieren“, macht Hornhuber klar. Bevor Mould & Matic die Serienwerkzeuge fertigt, baut das Unternehmen zunächst Testwerkzeuge und optimiert auf diesen das Endprodukt.
Die Möglichkeit, verschiedene Produktgrößen und Werkzeugkonfigurationen einzusetzen, war jedoch noch nicht alles. Schnelle Werkzeugwechsel sollten realisierbar sein, die zur Not sogar ein Bediener alleine bewältigen kann. Ein Luftkissen-Rüstwagen für das Spritzgießwerkzeug und einer auf Rollen für das Blaswerkzeug machen den schnellen Wechsel möglich. Ein Hallenkran erübrigt sich. Die Werkzeugwechsel sind einfach. Mit dem Rüstwagen fährt der Bediener das Werkzeug an die Maschine heran und wechselt mittels eines Seilzugs und Rollenbahnen schnell und ergonomisch das Spritzgießwerkzeug. Zufrieden berichtet Hornhuber: „Ein vollständiger Werkzeugwechsel von Gutteil zu Gutteil dauert für einen geübten Techniker nur fünf bis sechs Stunden. Steht nur ein Wechsel der Blasform an, geht dieser in 30 Minuten über die Bühne.“
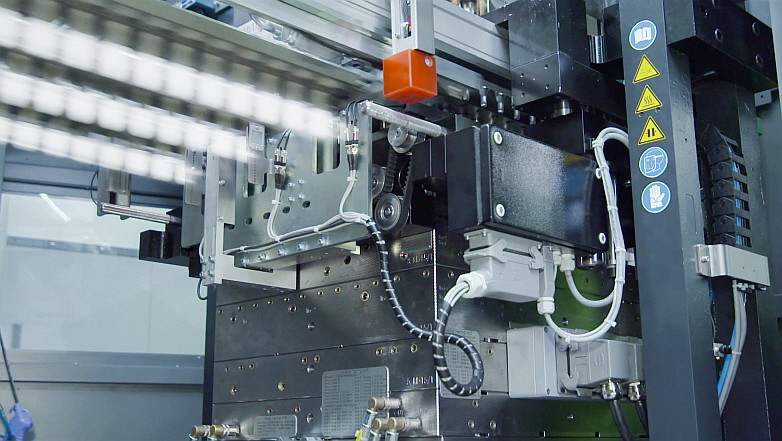 Dreireihiges Lineargreifersystem
Hohe Fertigungstiefe In der Praxis sind diese vielen kleinen Details Gold wert. Ein Kunde von Mould & Matic hat die ersten zwei Jahre vier verschiedene Artikel auf seinem Blowliner M gefertigt. Schnelle Werkzeugwechsel und hohe Flexibilität in Größe sowie Design der Vorformling- und Blaswerkzeuge waren da unabdingbar. Dann lief einer der Artikel aus. Von einem 30 ml Fläschchen musste er auf einen fünf Liter Behälter umstellen. „Kein Problem!“, erzählt Hornhuber. „Diese Vielfalt ist mit unserer Werkzeugtechnik ohne Schwierigkeit realisierbar.“
Bis auf die Spritzgießmaschine und das Heißkanalsystem kommen sämtliche Komponenten des Blowliners von Mould & Matic. Die gesamte Maschinensteuerung und Software stammen aus Micheldorf und sind in Beckhoff programmiert. Um die Prozesssicherheit zu optimieren, stehen Kamerainspektion der Behälter und eine Dichtigkeitsprüfung optional zur Verfügung. Das Unternehmen berät bei der Werkstoffwahl und beim Design der Vorformlinge und Flaschen. Denn die Vorformlinge bestimmen die Zykluszeiten des Streck-Blas-Prozesses, die Materialverteilung im Endprodukt und damit Wanddicken. Hornhuber bekräftigt: „Intelligentes Vorformlingdesign spart bares Geld. Denn damit können wir Materialeinsparungen und höhere Zykluszeiten realisieren.“
Auf dem Blowliner M sind Zykluszeiten von zehn Sekunden möglich, der kleine Bruder Blowliner S schafft es sogar in unter acht Sekunden. Damit steht dem Markt eine Spritz-Streck-Blas-Technologie zur Verfügung, die hinsichtlich Qualität, Flexibilität und Produktivität in der ersten Liga spielt.
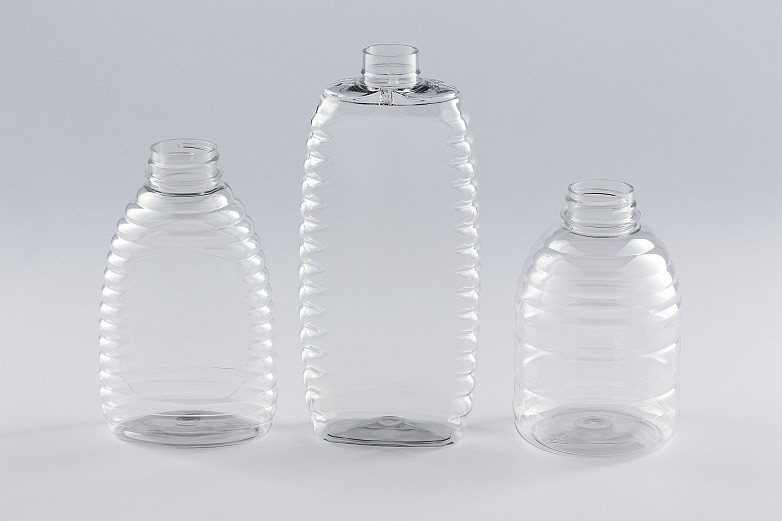 Produktmuster Blowliner
Höhere Qualität bei geringeren Kosten. Neues FLF-Vakuumkaschierverfahren von Kiefel mit Millionen Euro Einsparpotential.
Was wäre der Innenraum eines Fahrzeuges ohne optisch ansprechende Oberflächen bei Türen, Mittelkonsole und Armaturenbrett? Je höher die Fahrzeugklasse, desto hochwertiger fallen die Innenraumverkleidungen aus. Strukturen in der Oberfläche, eine angenehme Haptik und alles mit einer hohen Fertigungsqualität produziert sind Forderungen, die die Branche selbstverständlich stellt. Gleichzeitig steigt der Kostendruck für den Bereich Interieur stetig an. Ein neu konzipiertes Vakuumkaschierverfahren von Kiefel ist die Antwort auf diese Herausforderungen.
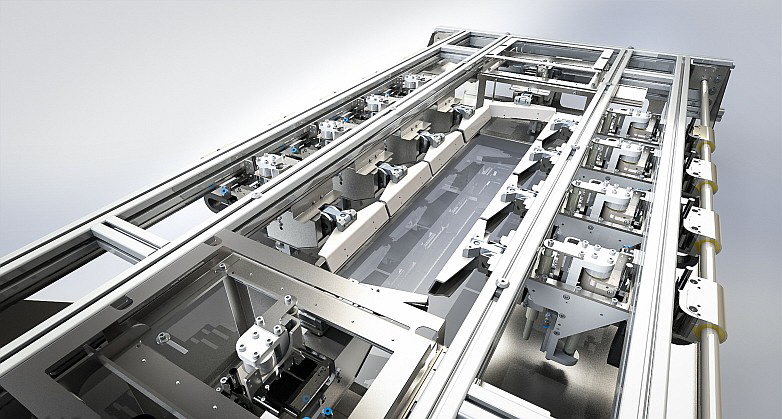 Linearantrieb - einsetzbar beim Vakuumkaschieren, IMG-Kaschieren und Presskaschieren
Vakuumkaschierverfahren bringen die Folien auf die Innenraumverkleidungen. Um die Bauteilkosten deutlich zu senken, hat die KIEFEL GmbH, Freilassing, eine ganzheitlich innovative Technologie entwickelt und dazu sämtliche Prozessschritte unter die Lupe genommen sowie optimiert. Herausgekommen ist ein einzigartiges Vakuumkaschierverfahren - die Flexible-Lamination-Frame (FLF)-Technologie. Mit der FLF-Technologie gelingt es den Freilassingern, den Materialverbrauch und damit die Folienkosten um rund 40 Prozent im Vergleich zu herkömmlichen Vakuumkaschierverfahren zu senken. Auch der Folienauszugsgrad wird deutlich verringert und reduziert sich auf lediglich 10 bis 15 Prozent. Folglich kommt das FLF-Vakuumkaschierverfahren nahe an die Qualität der Oberfläche heran, die mit der InMold-Graining Kaschiertechnologie erreicht wird. Auf diese Weise stellt sie eine klar kostengünstigere Alternative dar.
Doch was steckt hinter dem neuen FLF-Verfahren? Die Innovation liegt in der Verwendung exakter Folienzuschnitte für jedes Bauteil, sodass kaum Verschnitt bei den Kaschierfolien anfällt. Das Herz des Verfahrens ist ein speziell entwickeltes, dreidimensional im Raum verfahrbares Greifersystem. Dieses positioniert die Folie auszugsfrei auf dem Trägerteil, bevor das Werkzeug schließt und Folie sowie Trägerteil verklebt werden.
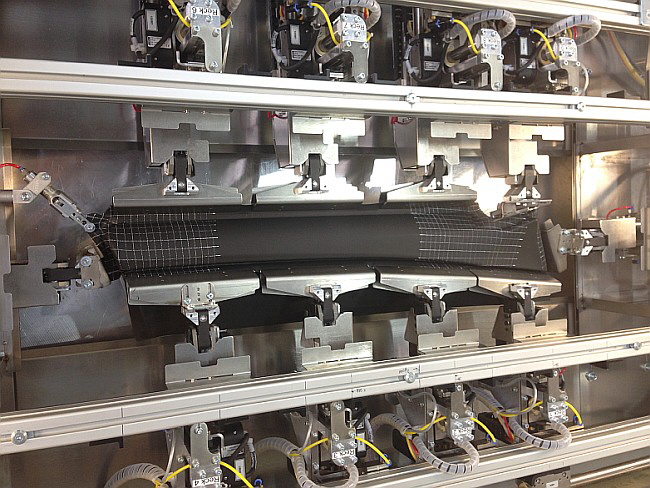 FLF mit kaschierten Teilen
Blick in den Prozess Ein hochflexibles, modular aufgebautes Anlagenkonzept mit einem hohen Automatisierungsgrad ermöglicht eine personalarme Fertigung. Die Materialen, wie Exakt-Zuschnitte und Trägerteile, kommen von vorgelagerten Prozessen, wenn möglich schon positioniert. Die weiteren Schritte übernehmen Roboter.
Durch die Integration von nachfolgenden Arbeitsschritten wie Stanzen und Kantenumbug steht am Ende der Linie ein fertiges Bauteil zur Verfügung. Im Vergleich zu konventionellen Fertigungsverfahren ist die gesamte Aufstellfläche wesentlich geringer. Es lassen sich bis zu 50 Prozent an teurer Produktionsfläche einsparen.
Kostensenkungen in Millionenhöhe „Der Clou der neuen Technologie liegt zweifellos bei der Folieneinsparung mit einer verbesserten Qualität der Oberflächen. Damit verbunden ist eine Kostensenkung des Bauteils, die sich über die Produktionsperiode einer Modellreihe schnell auf mehrere Millionen Euro aufsummiert“, so Wolfgang Eglseer, Kiefel-Vertriebsleiter Automobil. Die FLF-Technologie entspricht darüber hinaus auch in Bezug auf Automatisierung und Reduktion der Aufstellfläche den aktuellen Anforderungen aus der Automobilindustrie.
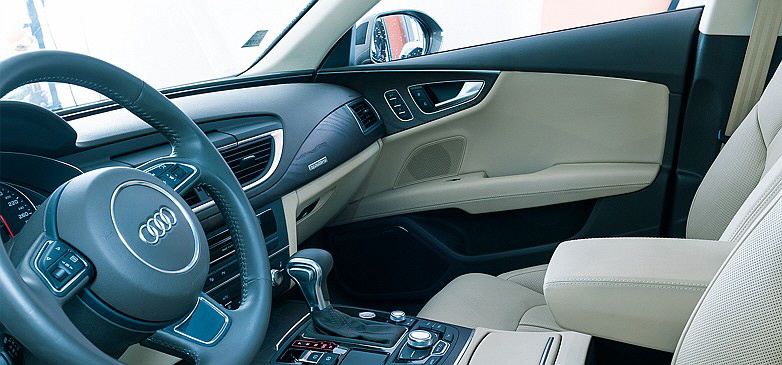 Höchste Qualität bei Premiumfahrzeugen
Besuchen Sie uns auf der Fakuma. Wir freuen uns auf Ihren Besuch an unserem Stand: Halle A1 / Stand 1325
|